Automatic Precoat Filter
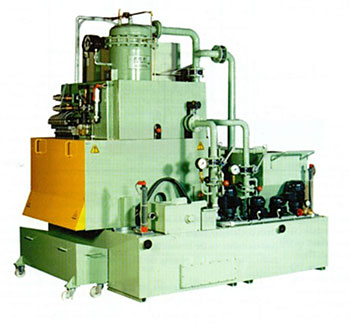
Automatic Precoat Filter are used for the cleaning of contaminated cutting fluids in metal processing and rolling mill applications. Clean cutting fluids lead to longer tool life, improved surface quality of workpieces or rolled goods, and efficient heat dissipation at the processing or forming point.
- Fully automatic operation
- Excellent filtration results
- Compact size
- Low maintenance requirements
- Full-flow filtration
- Dry cake discharge with minimal carryover of cutting fluid
- No fleece consumption
- Maximum lifespan of cutting fluid
The cleaned cutting fluid is supplied to the filter system pump (1) from the clean tank (2) of the processing machine. The contaminated cutting fluid is introduced into the dirt tank (3) of the cake filtration system through inlet channels or lifting stations. The internal processing of the system consists of four steps: “Cake Formation,” “Filtration,” “Regeneration,” and “Sludge Treatment.”
The cake pump (4) delivers clean medium from the filled cake tank (5) through the cake inlet (6) into the filter dome (7), passing through the filter candles (8). The filter aid, previously dosed into the cake tank through the dosing device (9), adheres to the stainless steel filter candles (8) and forms the actual filtration layer. The excess cutting fluid is returned to the cake tank (5) through the cake outlet (10). This “cake formation cycle” continues until the filter aid is formed on the filter candles (8).
After the cake formation cycle is completed, the cake pump (4) stops, and the cake outlet (10) is closed. Simultaneously, the filter pump (11) starts, and the filtrate outlet (12) is opened. The filter pump (11) then delivers cleaned cutting fluid from the filter dome (7) and the coated filter candles (8) through the filtrate outlet (12) into the clean tank (2) of the system. The dirt from the contaminated cutting fluid is retained on and within the filter cake layer. As the deep-filtering cake layer becomes more and more clogged, the differential pressure in the filter dome (7) increases. The filter dome pressure is monitored by the attached contact pressure gauge (14) and triggers the regeneration process at an adjustable pressure.
Regeneration:
Once the regeneration is triggered by the contact pressure gauge (14), the filter pump (11) stops, and the filtrate outlet (12) is closed. The sludge valve (15) is opened, and the filter dome (7) is reverse-blown with compressed air (16) against the filtration direction. The blown cutting fluid, along with the spent filter aid and deposited sludge, is directed to the secondary treatment or optionally in a designated regeneration tank (17). After the filter dome (7) is completely cleaned, the cycle in the cake filtration system restarts with the cake formation phase. The sludge present in the secondary treatment (17) is dried or dehydrated parallel to the renewed cake formation and filtration.
Sludge Treatment / Renewed Cake Formation Cycle:
Within the secondary treatment (17), solid components are retained, and the cutting fluid is recovered. The dehydrated solid is automatically discharged into a sludge bucket (18), while the recovered cutting fluid is returned to the system. The optimal design of the tank volumes and coordination of all pumps ensure continuous supply of finely cleaned cutting fluid to the connected processing machines. Each system is tailored and designed to meet the needs of the future operator to achieve optimal operating results.
The standard equipment of a compact system includes:
- Tank divided into dirt, clean, and cake tanks, including an optical oil level monitor with integrated switching function
- TÜV-approved cake filter dome equipped with wire mesh filter candles (stainless steel)
- Secondary treatment without fleece consumption
- Dosing device for filter aid
- Filter, system, and cake pumps
- Compressed air monitoring
- Control cabinet with PLC
- Mobile sludge bucket
- Execution according to operator-specific plant regulations
- Operation and maintenance manual
- Complete pneumatic and electrical installation
- Execution according to § 19.1 WHG (German Water Resources Act)
- CE marking
- Commissioning and operator training
Optional additional devices:
- Magnetic filter roll for pre-separation of ferritic coarse particles, including sludge box
- Immersion cooling unit
- Oil mist extraction
- Dust-free filter aid bag emptying to minimize excessive dust emissions
- Police filter in the system supply line
- Execution according to operator-specific factory regulations
- Lifting station for low machine beds and ground-level installation
Fully automatic cake filtration systems are used for the fine cleaning of cutting fluids and ensure optimal care of the media used. This results in extended lifespan of the cutting fluid and excellent machining results. They have proven themselves in various industries, such as superfinishing, microfinishing, fine grinding, or other machining processes that require optimal cutting fluid maintenance. Fully automatic compact systems are used for supplying individual machines and machine groups and are designed as full-flow systems. They are available in various sizes, with standard configurations achieving filter areas of up to 10 m². Special designs are possible within a certain range of variation, and centralized cake filtration systems are also available.
Filter types based on filtration fineness and specific filter performance:
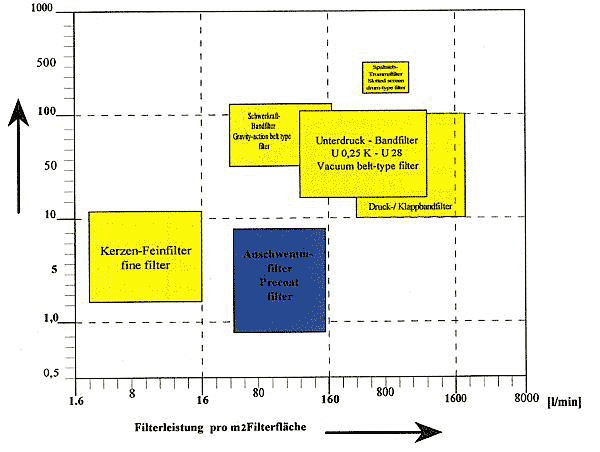
Note: The specified flow rates are filter-specific basic performance values and serve as guidelines for interested operators.
Our Service
Each filter system is specifically designed and customized for the specific application. We utilize our experience, in-house laboratory tests, as well as portable pilot plants for on-site testing at your company.